
Key features of RPU technology
Feasible to get GRS certificate
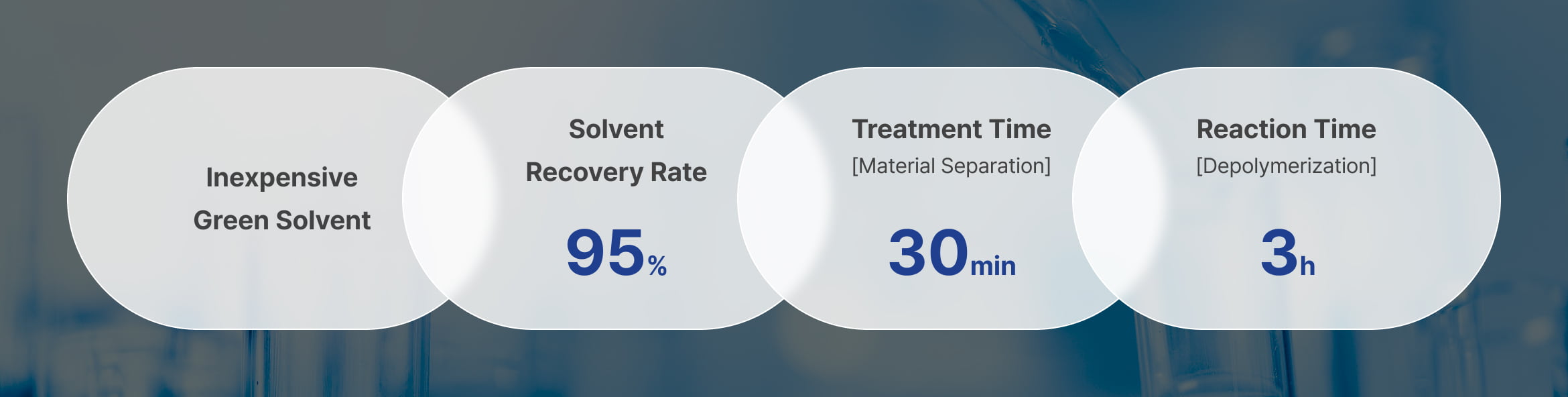
95% Purity
95% Recovery rate
1/15 CAPEX
ALL Feedstock flexibility
-50% GHGs Reduction
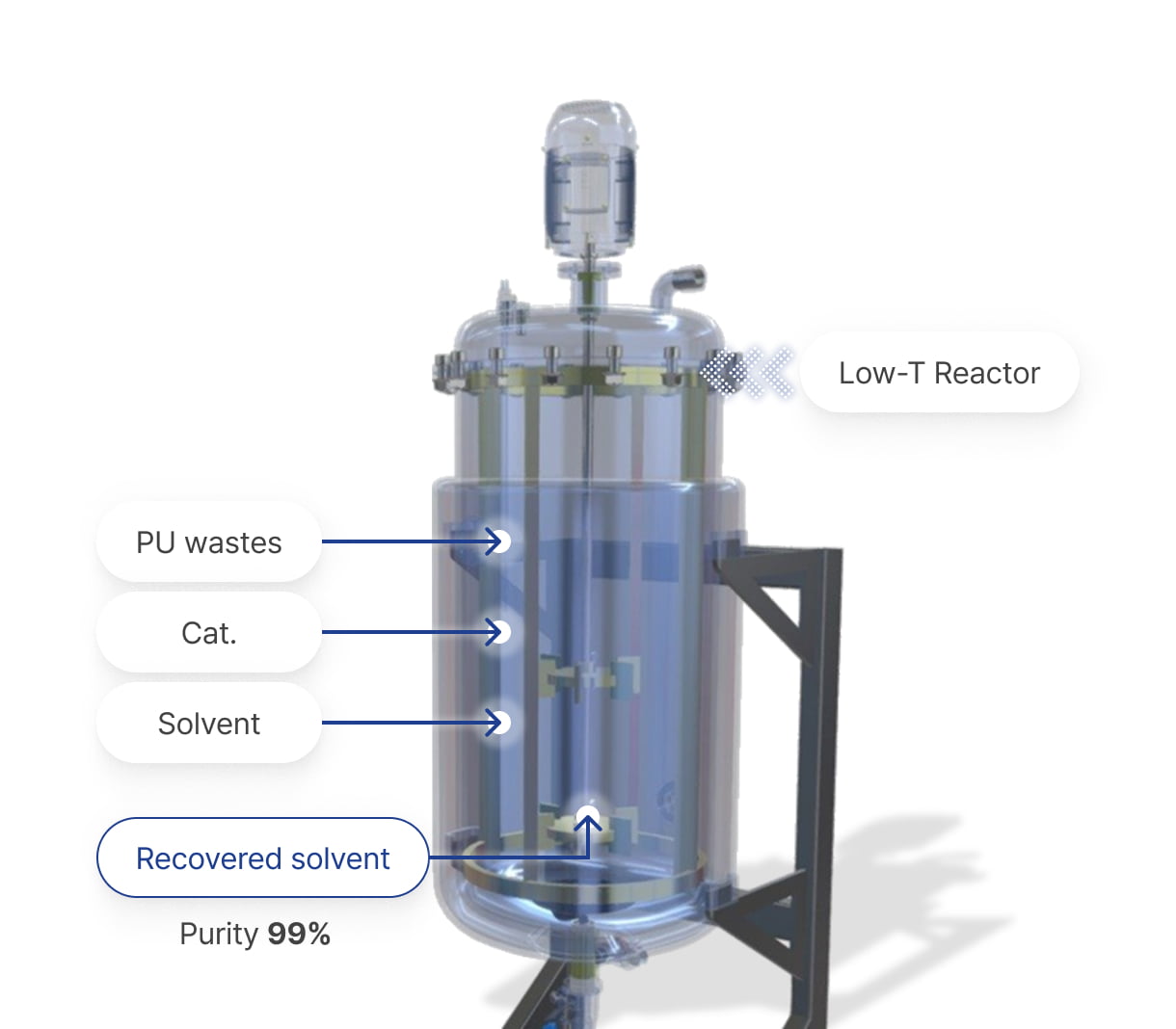
Our technology vs. traditional recycling approaches
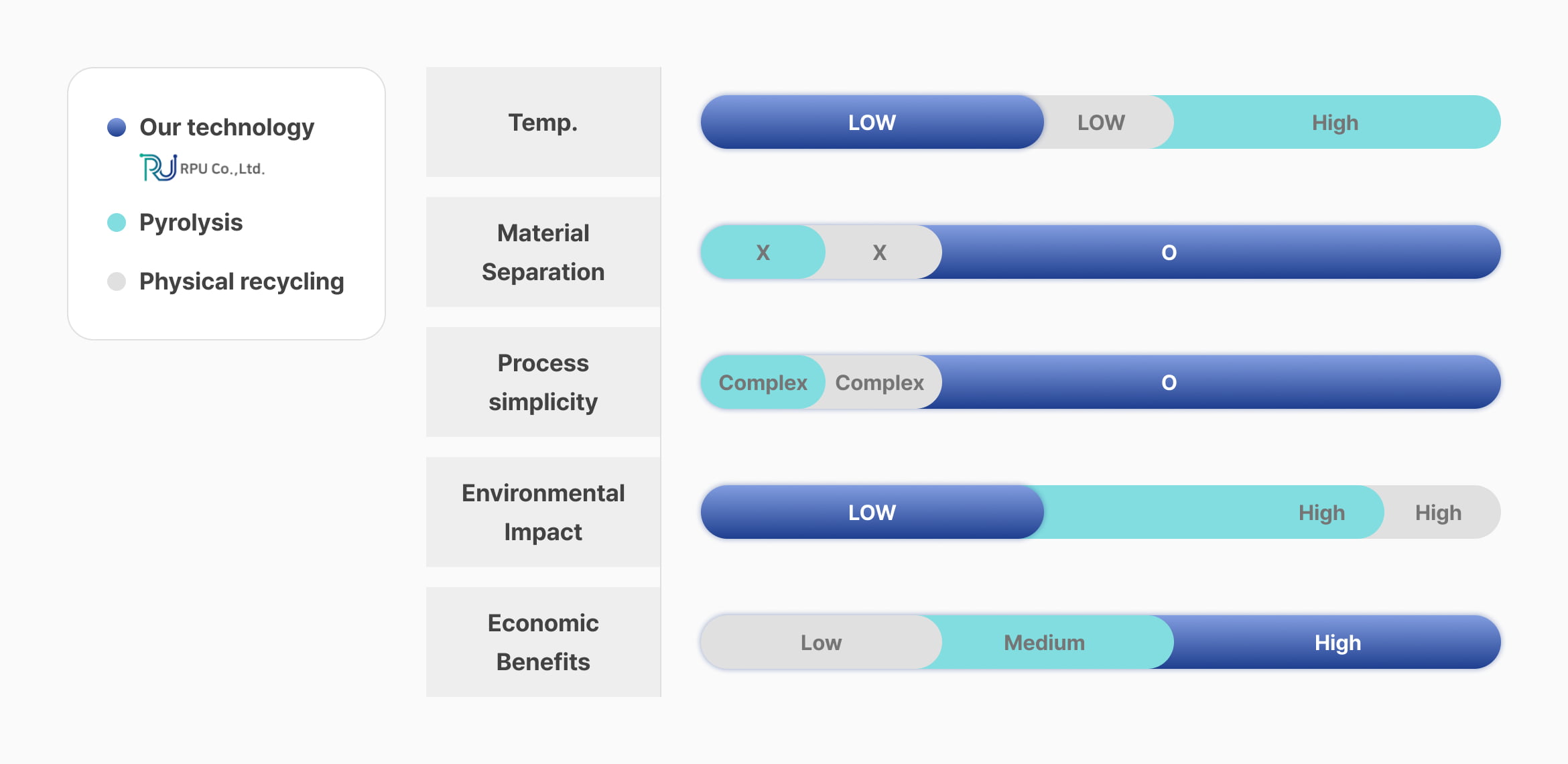

RPU Depolymerization
Technology
We specialize in polyurethane depolymerization using a low-temperature catalytic process (glycolysis).
This technology allows for the efficient production of high-purity monomers and building blocks with low-cost catalysts,
all within a short reaction time of 1 to 3 hours, ensuring both cost-effectiveness and sustainability.
Catalytic depolymerization of separated polymer (PU) at a low-T (150°C)
Low-cost catalysts
High purity monomer and building blocks products
Short reaction time (1~3 h)
Depolymerization of Flexible Polyurethane
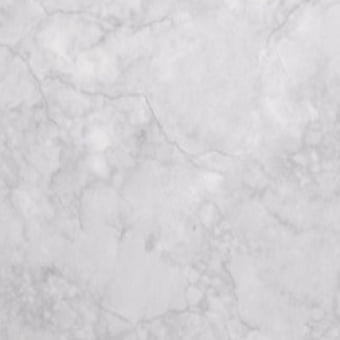
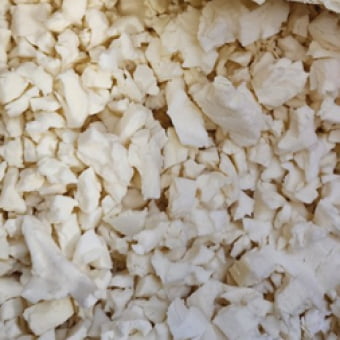
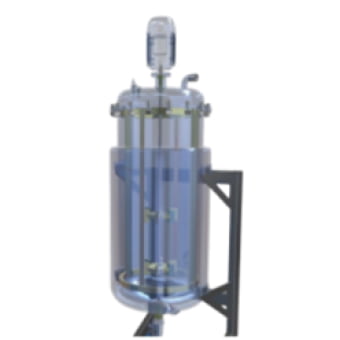
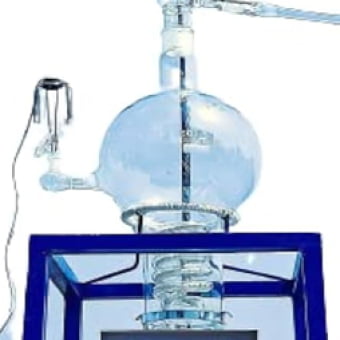
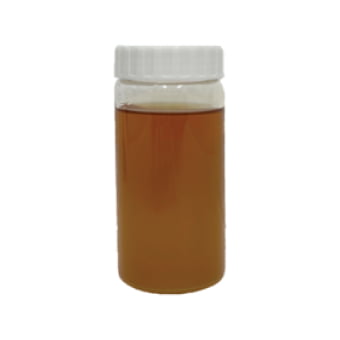
Flexible PU MAT
Crushing
Depolymerization
Purification
REPU-POL F3
Characterization of
REPUPOL R3
Recovery rate (%) 94.8
Specific density 1.074
Viscosity at 25°C 6,215
OH number (mg KOH/g) 321.2
Amin value (mg KOH/g) 150.5
Acid value (mg KOH/g) -
1H-NMR spectrum of
REPUPOL
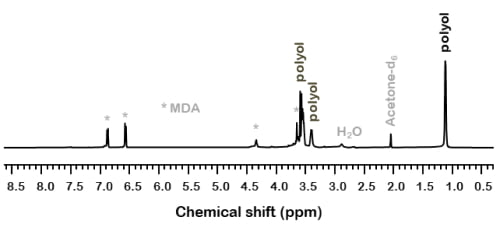
ATR-IR spectrum of
REPUPOL
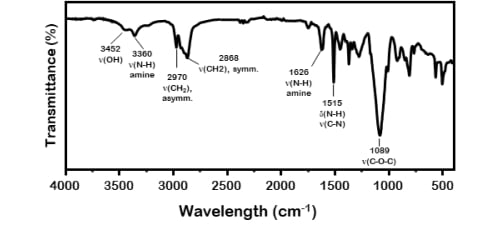
Automotive seat cushion
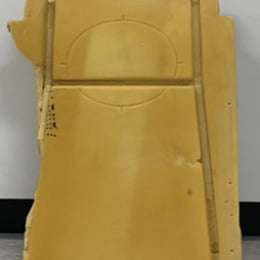
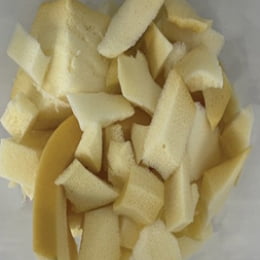
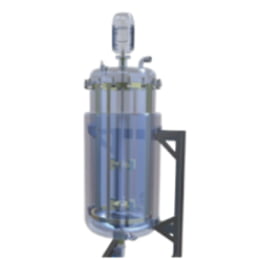
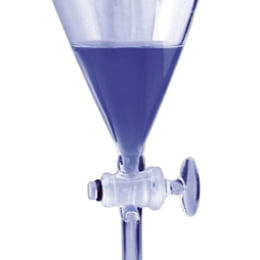
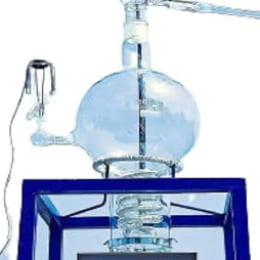
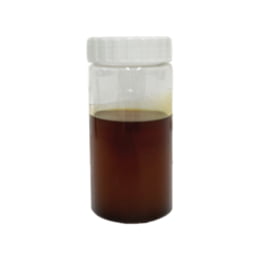
Flexible PU Automotive seat cushion
Crushing
Depolymerization
Separation
Purification
REPU-POL F3
Sample Analysis Data
Recovery rate (%) 54.8
Specific density -
Viscosity at 25°C 1,674
OH number (mg KOH/g) 169.7
Amin value (mg KOH/g) 74.9
Acid value (mg KOH/g) 0.06
1H-NMR spectrum of
REPUPOL
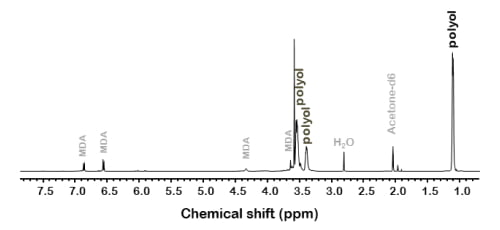
ATR-IR spectrum of
REPUPOL
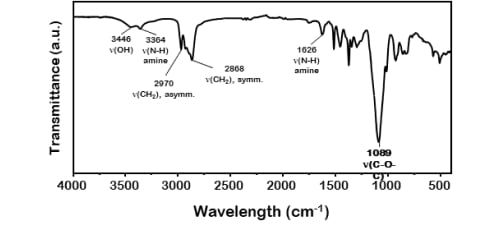
Depolymerization of Rigid Polyurethane
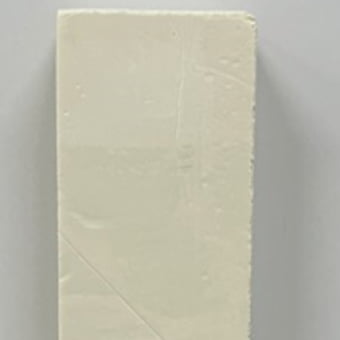
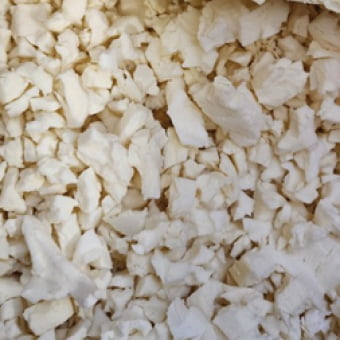

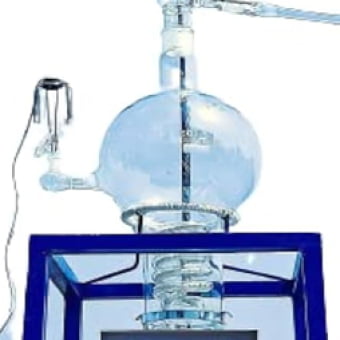
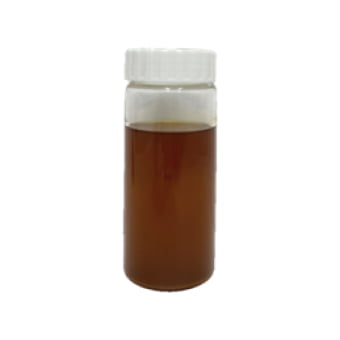
Rigid PU foam
Crushing
Depolymerization
Purification
REPU-POL R1
Characterization of
REPUPOL R3
Recovery rate (%) 87
Specific density -
Viscosity at 25°C 20,000~30,000
OH number (mg KOH/g) 403.2
Amin value (mg KOH/g) 207.9
Acid value (mg KOH/g) 0.59
1H-NMR spectrum of
REPUPOL
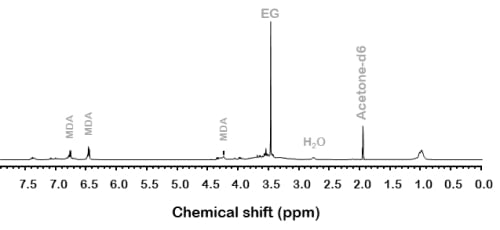
ATR-IR spectrum of
REPUPOL
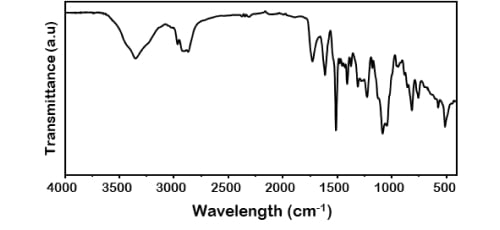
Foaming test based on recycled polyol content
Recycled polyol content |
Gell Time |
Tack Free Time |
Rising Time |
Rising Length |
Foam weight |
Density |
---|---|---|---|---|---|---|
![]() 1(5%) |
65 | 120 | 90 | 121 | 48.94 | 48.23 |
![]() 2(10%) |
58 | 135 | 76 | 11.8 | 48.21 | 48.38 |
![]() 3(15%) |
51 | 103 | 83 | 12.0 | 49.06 | 50.23 |

RPU Material Separation
Technology
Our technology uses a low-cost organic solvent to selectively dissolve polyurethane (PU) and nylon, while polyester remains solid.
High-purity nylon crystals are obtained through recrystallization,
enabling efficient recycling of synthetic fibers and composites in an eco-friendly and cost-effective way.
Inexpensive organic solvent is utilized to adjust the solubility of the polymers in textile blends, mixed plastic wastes
PU and nylon are completely dissolved in the liquid solution, while polyester remains as a solid
Pure nylon granules are obtained by recrystallization
How does it work
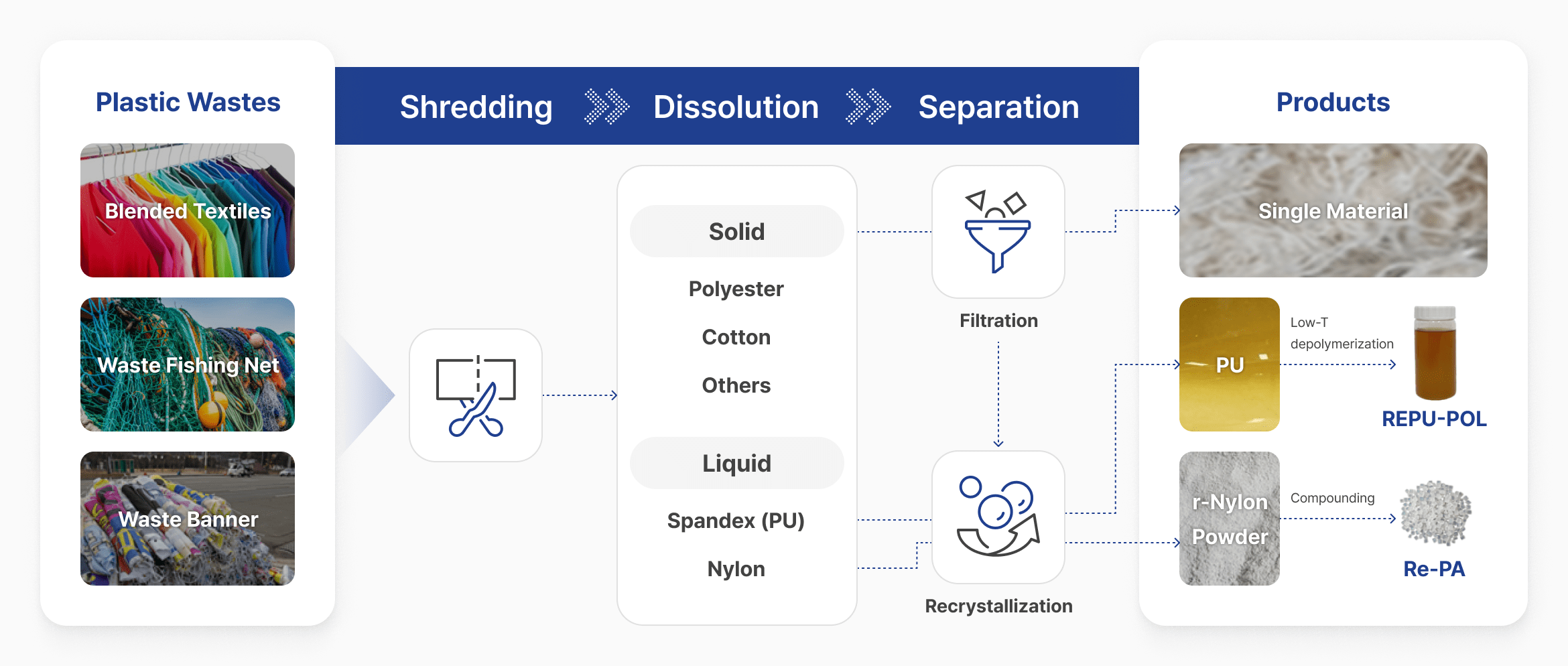
Separation of Nylon/Spandex
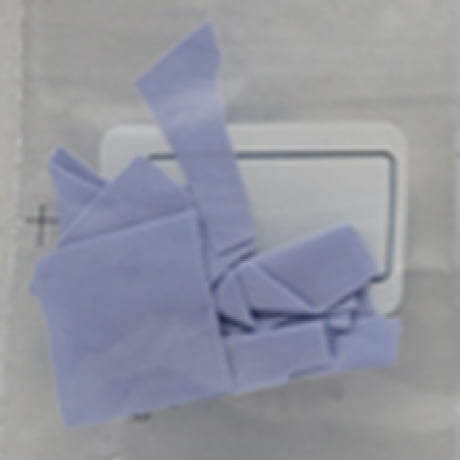
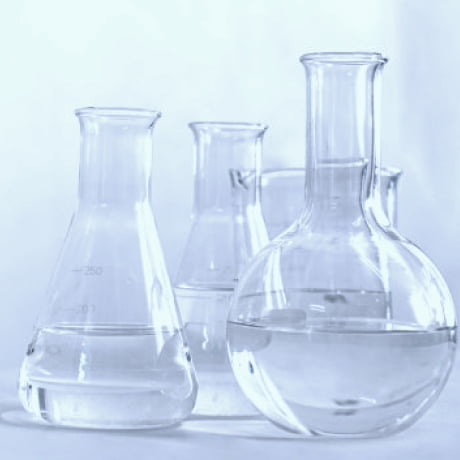
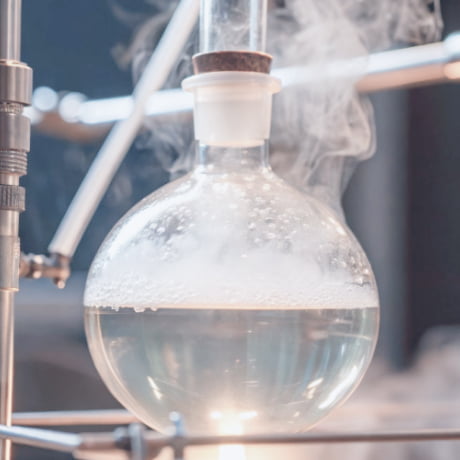
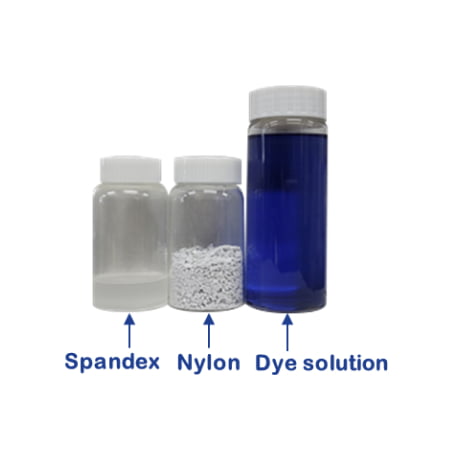
Nylon/Spandex Fabric
Dissolution
Recrystallization
Spandex/Nylon/Dye solution
1H-NMR Spectra
Recovered
Nylon 6

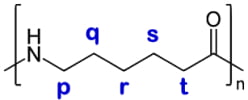
Structure of nylon 6
Recovered
Spandex

Nylon/Spandex
Blend

Separation of Fabric
01 80% Nylon / 20% Spandex
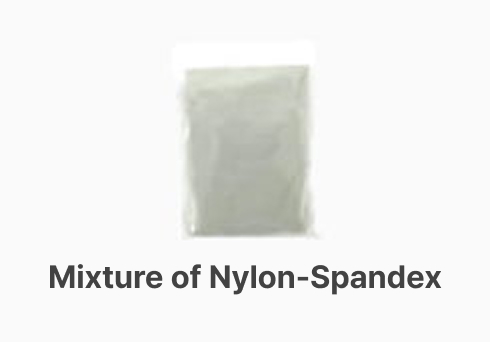
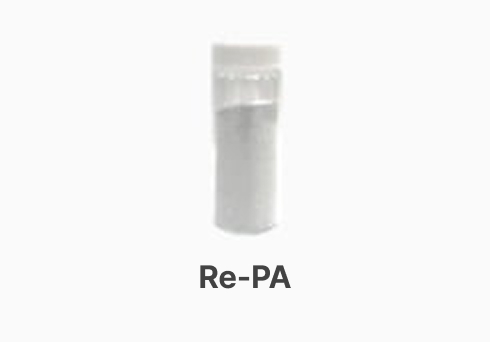
02 52% Nylon / 48% Spandex
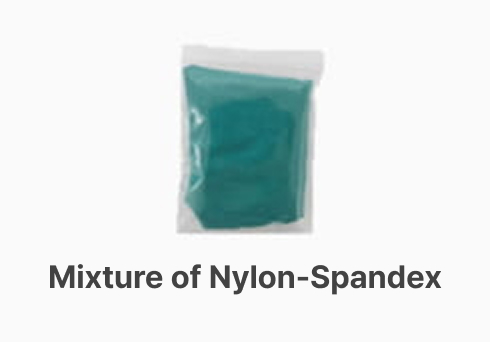
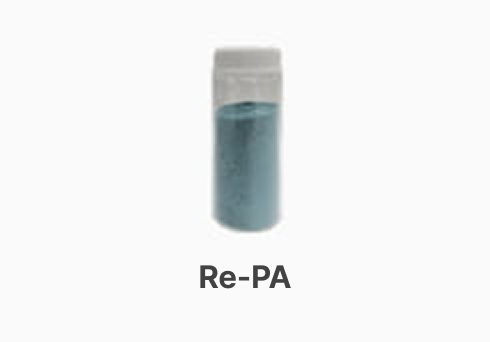
03 PU coated Nylon
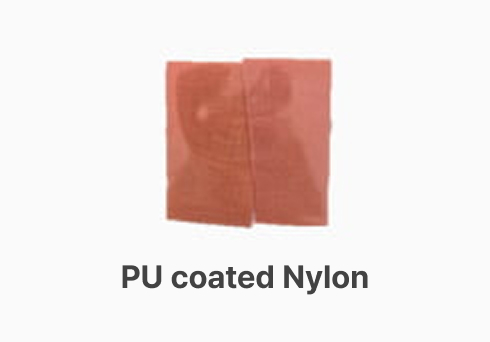
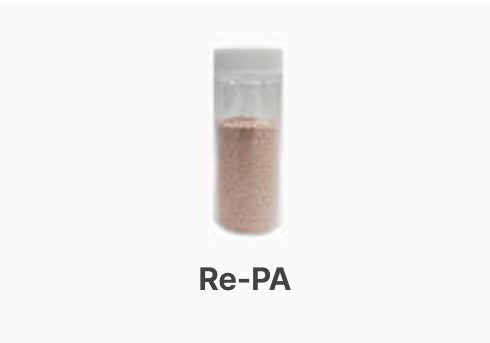
04 96% Cotton 4% Spandex
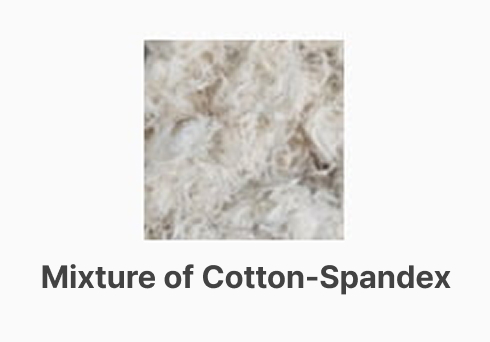
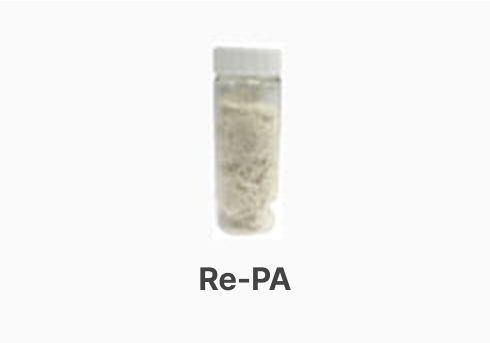
05 TPU / Nylon fabric
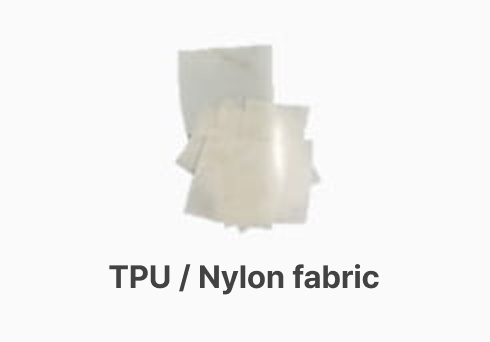
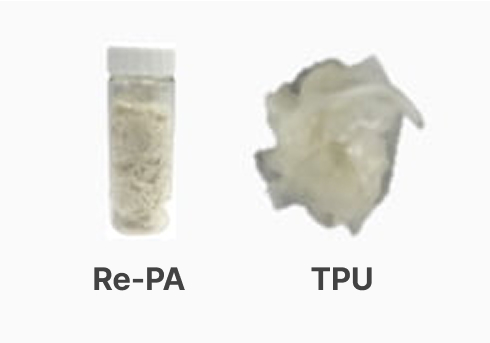
Separation of Waste fishing net
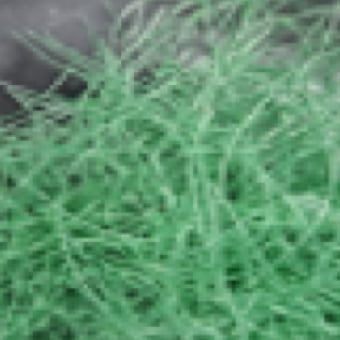
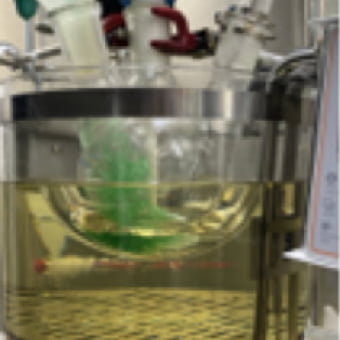
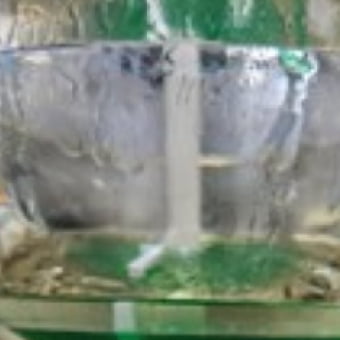
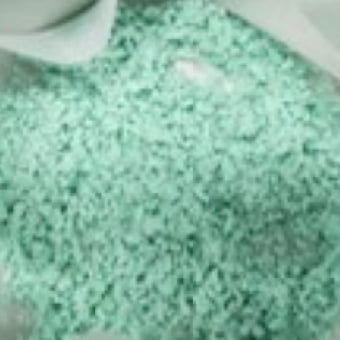
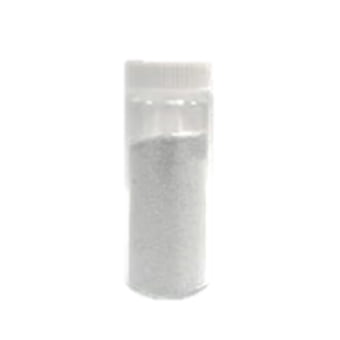
Waste fishing net
Solv. treated
Separate
Dye removal
Dried

RPU
Patents & Certifications
Patents
Certifications